Machine Guarding Meeting Kit
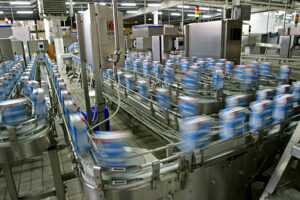
WHAT’S AT STAKE
Moving machine parts can cause minor injuries such as cuts and scrapes, major crushing and amputation injuries, and even death.
WHAT’S THE DANGER
DANGERS / HAZARDS – MAIN CATEGORIES
- Point of operation hazards occur where the machine work is actually done on the material such as cutting, shearing, pressing, punching, or forming. These machines require a guard that prevents the operator’s hands or fingers from coming near the point of operation. The guards can include physical shields or barriers, laser sighted power controls, and even operator restraints that limit the movements of hands and arms.
- The in-running side of rolling equipment can pull fingers, hands, and arms into machines. Guarding for roll type equipment is required by using a fixed or self-adjusting barrier that allows material through but prevents body parts from entering. Machine braking and emergency shutoff bars also control rolling hazards.
- Rotating machinery poses a threat of injury, amputation, scalping, and death. Rotating parts require guards or shields to prevent accidental contact. Never wear gloves, neckties, jewelry, lanyards, or loose-fitting clothing that could become entangled. Tie back and secure long hair.
HOW TO PROTECT YOURSELF
- Assess the Risk. Conduct hazard assessment.
- When the machine is first installed.
- At least monthly or more often if the manufacturer recommends it.
- After injuries, near misses and other incidents.
- After the machine malfunctions or is moved.
Cover the four areas where machine injuries are most likely to occur:
- The point of operation, or machine part where the cutting, shaping, boring, forming or other operation is done on the material.
- Moving parts, including flywheels, pulleys, belts, couplings, chains, gears, conveyors, feed mechanisms, etc.
- In-running nip points, or spaces between rotating and/or slowly moving parts.
- Primary power source, including engines, turbines and other equipment used to power the machine.
- Select Guards. Basic types of machines guarding methods that can use alone or in combination.
- Interlocked guards – automatically stop the machine when a tripping mechanism is activated until the guard is back in place
- Self-adjusting guards – here the size of the opening in the barrier adjusts to accommodate the stock/material
- Automatic stopping devices – such as presence sensing devices and pullback devices
- Automatic or robotic feeding and ejection so that materials don’t have to be manually fed into and taken out of the machine
- Location/Distance guarding – placing machines away from work areas and/or in locations that are impossible or difficult for workers to get to
- Inspect Guards
Once machine guards are in place, they must be properly and regularly inspected to ensure they are:
- Firmly secured so that they can’t easily be removed.
- Free of jagged edges, shear points, unfinished surfaces, and other hazards.
Ensure inspection covers:
- Guards used at the point of operation
- Guards at the power source
- Each continuous line of shafting
- Pulleys, ropes, belts, chains and chain drivers, sprockets, and gears
- Provide Training
When performing tasks, you must understand:
- The hazards posed by the machines at your workplace.
- How machine injuries can happen
- The guards in place to control the hazards.
- Never, ever remove or tamper with machine guards.
- The kind of clothing to wear to avoid machine injury.
- The PPE to use when working near machines.
FINAL WORD
A good rule of thumb is “If it moves, guard it.” Take time and work to conduct a job hazard analysis and identify danger points. Be alert to your surroundings and of how close you are to moving machinery. Staying clear of a pinchpoint, driveshaft or set of rollers may save your life limb.