Aerial Devices and Manlifts – Quick Tips
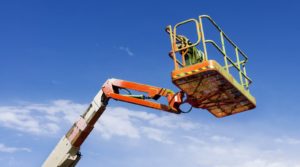
Aerial Devices
Aerial devices are vehicle-mounted, elevated and rotating work platforms. OSHA defines a vehicle as any carrier that is not manually propelled and a platform as any personnel-carrying device (basket or bucket that is a component of an aerial device. Vehicle-mounted devices—telescoping, articulating or both—used to position personnel are considered aerial devices. This includes extensible and articulating boom platforms, aerial ladders, vertical towers and a combination of any of the above. Regulations regarding these platforms are found in 29 CFR 1910.67.
Manlifts
A manlift is a device consisting of a power-driven, end-less belt that moves in one direction only. It usually includes steps or a platform with attached handholds and transports personnel from floor to floor. Manlifts are covered under 29 CFR 1910.68.
General Requirements
Aerial devices (aerial lifts) acquired on or after July 1st, 1995 shall be designed and constructed in accordance with ANSI A92.2-1969, Vehicle- Mounted Elevating and Rotating Work Platforms. These lifts may be modified for uses other than those intended by the manufacturer, provided the modification has been certified in writing by the manufacturer or a testing agency and conforms with all applicable provisions of the ANSI standard.
All new manlifts shall meet the design requirements of ANSI A90.1-1969, American National Safety Standard for Manlifts. The OSHA regulations apply to manlifts used to carry only personnel that are trained and authorized by the employer, and do not cover moving stairways, elevators with enclosed platforms, gravity lifts nor conveyors used only for conveying material.
Specific Requirements for Aerial Devices
Summary of OSHA Standard 29 CFR 1910.67: Before a vehicle is moved for highway travel, aerial ladders shall be secured in the lower traveling position. Lift controls for extensible boom platforms shall be tested each day prior to use and used only by trained individuals. A body belt for positioning shall be worn with a lanyard attached to the boom or basket when working from an aerial lift. Belting off to an adjacent pole or structure is not permitted.
When preparing an aerial lift for use, brakes shall be set, and outriggers (when used) shall be positioned on pads or a solid surface. If the lift will be used on an incline, wheel chocks must be installed beforehand. Once a boom is elevated in working position with people in a basket, the vehicle may not be moved unless such equipment is specifically designed for this type of operation.
Articulating and extensible boom platforms designed as personnel carriers shall have both upper controls on the platform and lower controls at vehicle or ground level. Although lower controls shall be able to override upper controls, lower level controls shall not be operated unless permission has been obtained from the employee in the lift, except in case of an emergency.
Safety testing, including electrical tests and bursting safety factors for hydraulic and pneumatic components must comply with the requirements of ANSI A92.2-1969. Any welding operations must conform to the American Welding Society (AWS) Standards, specifically:
- Standard Qualification Procedure, AWS 0-41
Recommended Practices for Automotive Welding Design, AWS D8.4-61 Standard Qualification of Welding Procedures and Welders for Piping and Tubing, AWS D10.9-69
Specifications for Welding Highway and Railway Bridges, AWS D2.0-69
Special Design Requirements for Manlifts
The OSHA standard specifies several requirements for the location and design of manlifts. The following is an overview of each requirement:
Floor openings: Sizes of floor openings are dependent on the size of belt in use. All openings need to be uniform in size and approximately circular.
Landings: Clearance between the floor and lower edge of the conical guard shall be at least 7′ 6″. Space next to openings shall be kept clear at all times and shall provide safe footing at all times. Lighting of at least five foot candles shall be provided at each floor landing. Floor or emergency landings shall be provided every 25 feet or less.
Guards on underside of floor openings: A bevel guard or cone shall be provided on the ascending side of the floor opening.
Protection of entrances and exits: Entrances and exits at all floor landings to manlifts shall be guarded by a maze (staggered railing) or handrail equipped with self-closing gates. Rail construction must comply with ANSI A12.1-1967, Safety Requirements for Floor and Wall Openings, Railings and Toeboards and 29 CFR 1910.23.
Guards for openings: Openings shall be guarded on all sides not used for movement by a wall, railings or panels. Guards shall be at least 42″ high on up-running sides and 66″ high on down-running sides.
Bottom arrangement: Specific design requirements cover location and maintenance of the bottom landing, lower pulley, mounting platform and location of guardrails.
Top arrangements: There must be a top clearance of at least 11′ above the top terminal landing and a clearance of at least 5′ between the center of the head pulley shaft and any ceiling obstruction. If the distance to the head pulley is more than 6′ above the top landing, an emergency grab rail or bar must be provided at the head pulley.
Illumination: Both up and down runs of a manlift shall be illuminated at all times when the lift is in operation.
Weather protection: The entire manlift and its driving mechanism shall be protected from the weather at all times.
Mechanical Requirements for Manlifts
Brakes: Brakes used for stopping and holding shall be inherently self-engaging with an external source to disengage. The brake shall be electrically released and capable of stopping and holding the manlift when the descending side is loaded with 250 pounds on each step.
Belt: Belts shall be strong enough to meet ANSI A90.1-1969 and have the following width requirements: not less than 12″ wide for a travel distance not exceeding 100 feet; not less than 14″ for a travel distance greater than 100 feet but less than 150 feet; and 16″ for travel distance exceeding 150 feet.
Speed: The maximum allowable design speed of a manlift is 80 feet per minute.
Platforms or steps: Steps must be between 12″ to 14″ deep and at least as wide as the belt to which it is attached. The distance between steps shall be equally spaced and not less than 16′ from the upper surface of one step to the upper surface of the next step above it.
Handholds: Handholds attached to the belt must be installed between 4′ and 4′ 8″ above the step tread. The grab surface shall not be less than 4 1/2″ in width nor less than 3″ in depth and shall provide 2″ of clearance from the belt. All handholds must be of the closed type.
Up limit stops: There must be two separate automatic stop devices to cut off the power supply and apply the brake when a loaded step passes the upper terminal landing.
Emergency stop: An emergency stop must be provided within easy reach of ascending and descending runs of the belt.
Instruction and warning signs: Conspicuous and easily read signs stating Face the Belt, Use the Handholds and To Stop Pull the Rope must be placed at each landing. Additional signs are required for top floor warning and visitor warning.
Operating Rules and Inspection of Manlifts
No freight, packaged goods, pipe, lumber or construction materials of any kind shall be handled on any manlift. Manlifts need to be inspected by a designated, competent person at intervals of not more than 30 days, and limit switches shall be checked weekly. These inspections must be maintained in a certification record.
Frequently Asked Questions
Q: What is the difference between an articulating boom and an extensible boom?
A: An articulating boom is raised and lowered by two or more hinged sections. An extensible boom is raised and lowered through a telescoping motion.
Q: Can spliced belts be used on manlifts?
A: A belt that has become torn while in use on a manlift shall not be spliced and put back in service.
Q: Can workers keep their lunches on a manlift?
A: No. An early OSHA ruling interpreted a lunch box as a packaged good, which is prohibited.
Source29
CFR 1910.67, Vehicle-mounted Elevating and Rotating Work Platforms
29 CFR 1910.68, Manlifts
ANSI A92.2-1969, Vehicle-Mounted Elevating and Rotating Work Platforms www.ansi.org
ANSI A90.1-1969, American National Safety Standards for Manlifts
American Welding Society www.aws.org
The information contained in this article is intended for general information purposes only and is based on information available as of the initial date of publication. No representation is made that the information or references are complete or remain current. This article is not a substitute for review of current applicable government regulations, industry standards, or other standards specific to your business and/or activities and should not be construed as legal advice or opinion. Readers with specific questions should refer to the applicable standards or consult with an attorney.
Source: Grainger Know How – https://www.grainger.com/know-how